Sand Casting
Why Choose Sand Casting?
Sand casting is the most commonly used casting process because of the cost effectiveness of the process and the availability of raw materials. Sand casting is a process where the molten metal is poured into a mould made of sand. It is best suited to low-volume or complex non-ferrous castings or large ferrous castings.
WELD2CAST Engineering is able to produce complex sand-casting moulds by hand using Greensand for smaller quantities and Resin or Petrol-Bonded Techniques using a semi-automated or automatic Horizontal Moulding Machine (DISAMATIC) process for larger quantities.
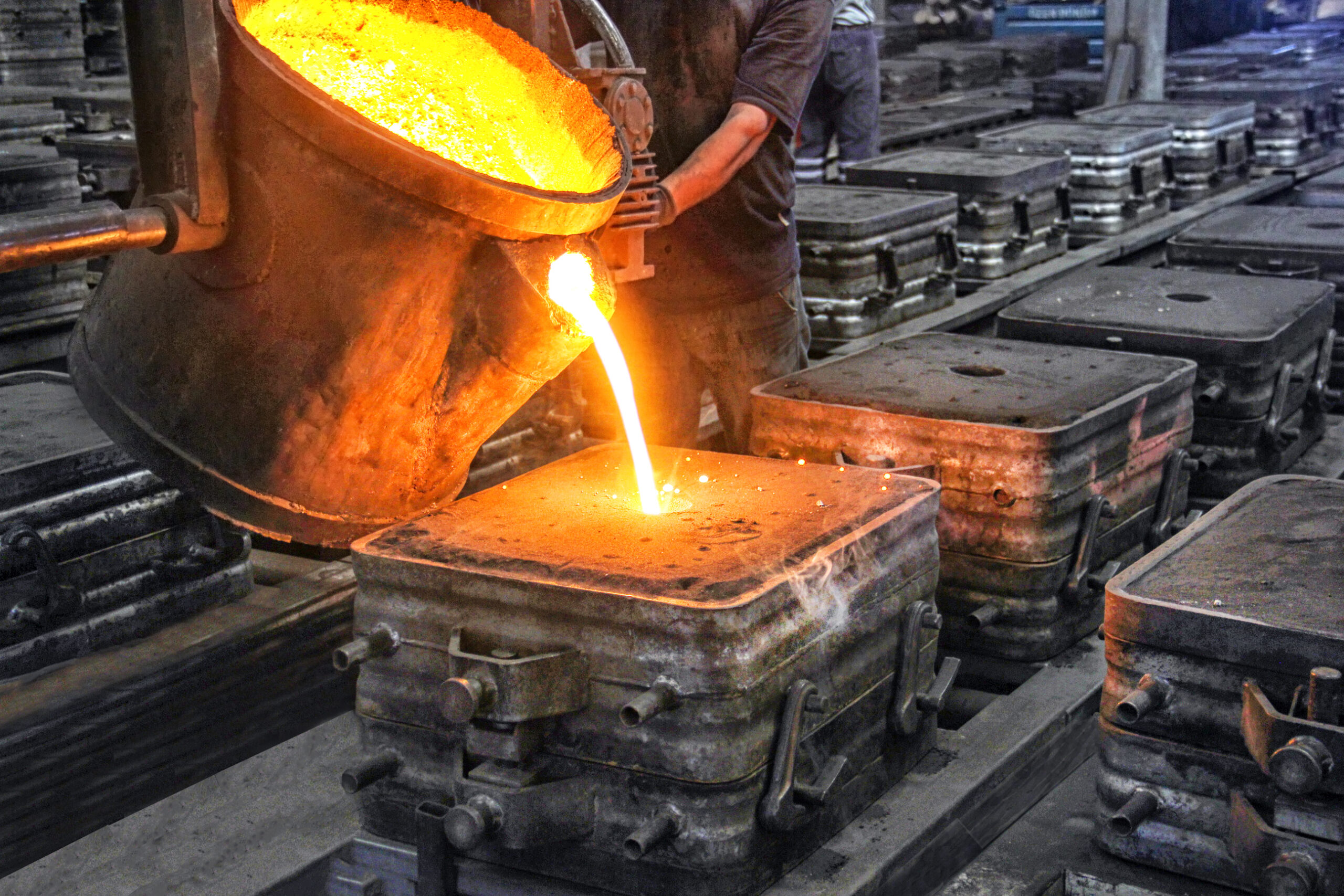
WELD2CAST’s Sand Casting Benefits Include:
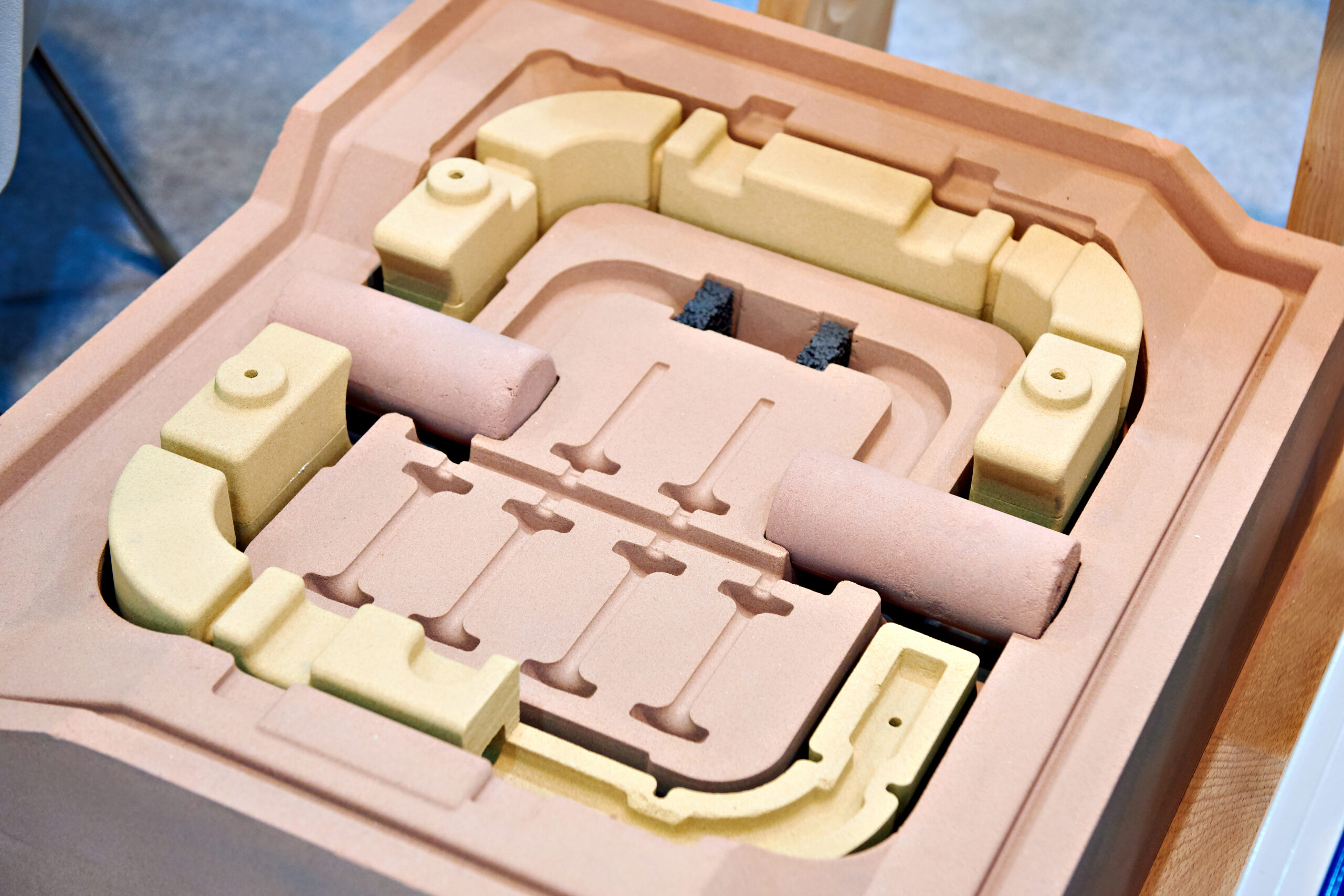
- Low tooling costs and fast set-up compared to other castings techniques.
- Complex and intricate castings can be achieved with multiple internal cores.
- Up to 75% of the sand used in the process is possible to reclaimed.
- High production efficiency (average of 200-300 units per hour).
- More flexible castings methods depending on quantities.
- Practically possible to cast any material, including those with a high melting point.
WELD2CAST Offers Various Sand-Casting Processes
WELD2CAST Engineering offers various sand-casting processes:
Hand Moulding
- Ideal option for very large sized parts
- Suitable for castings between 1 kg – Many ton
- Any annual quantity production runs, suitable for low volumes series
Semi-automatic Moulding Machines
- Suitable for size castings ranging from 2 kg to 150 kg
- Minimum of 1,000 units per year
- Very cost efficient per kg most significantly in the 20 – 60 kg item range
Automatic Horizontal Moulding Machine
- Suitable for castings between 1 kg – 80 kg
- Good surface finish and tight tolerances ISO 8062 / CT8
- Stable dimensions & mechanical properties because everything is runed in an automatic process. Ex. DISAMATIC automatic production.