High-Pressure Die Casting
Why Choose High-Pressure Die Casting?
The High-Pressure Die Castings process produces high volumes of identical, low-temperature metallic components with precision and repeatability. High-Pressure Die Casting requires complex machinery in order to inject molten metal or alloys at high force into a metal die – usually a hardened steel tool.
For Die Gravity Casting the process isn’t automated, in High-Pressure Die Casting it is. This process is suited to high production rates and can be performed at a low cost per unit. The most common alloys used are non-ferrous metals, such as aluminium, zinc and magnesium. WELD2CAST’s most popular alloy is aluminium A 380, due to its optimal combination of material properties and production workability. It is especially suitable for use in the following sectors: Electronic & Communication Devices, Automotive Parts, Structural Components, Furniture Parts.
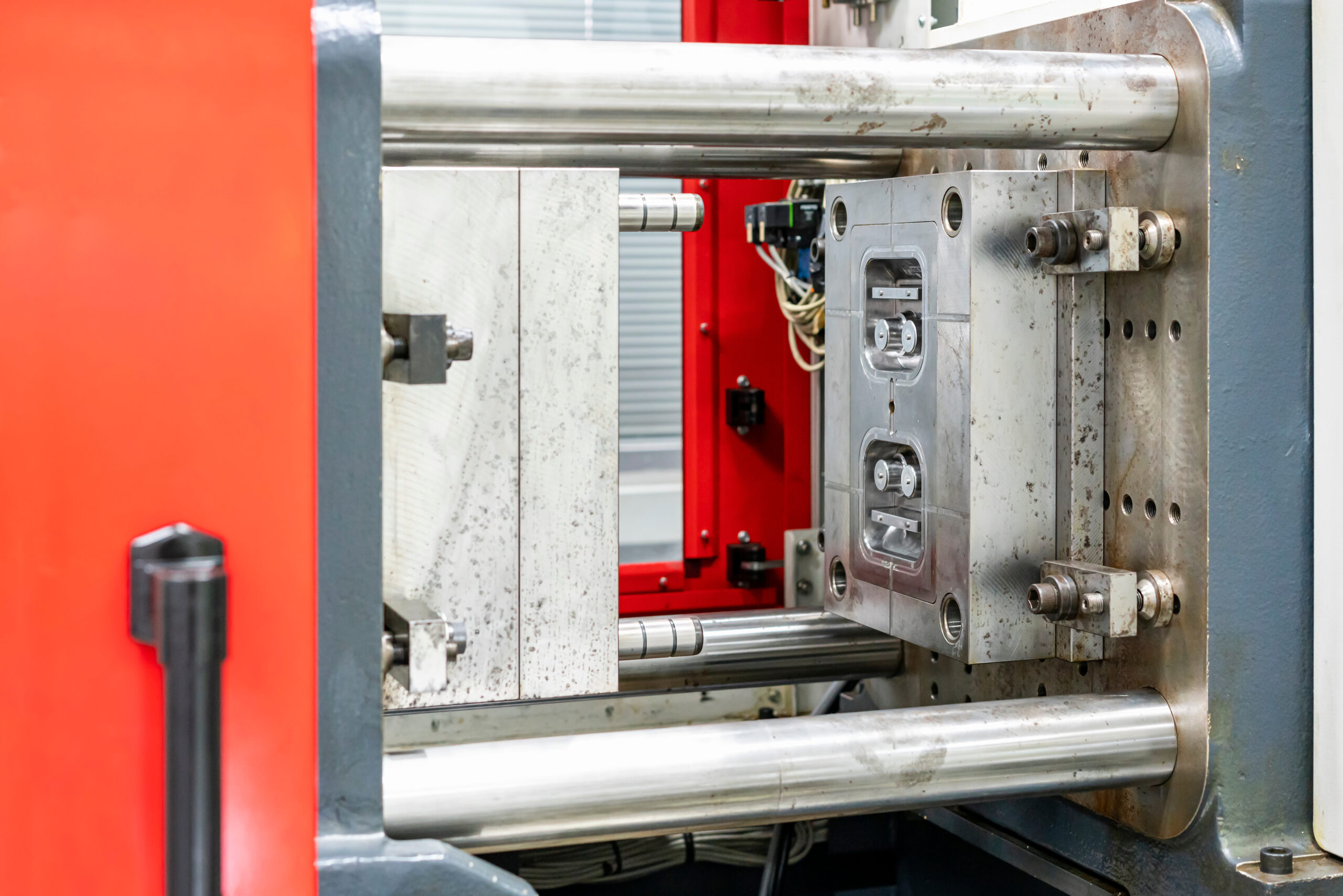
WELD2CAST’s High-Pressure Die Casting Benefits Include:
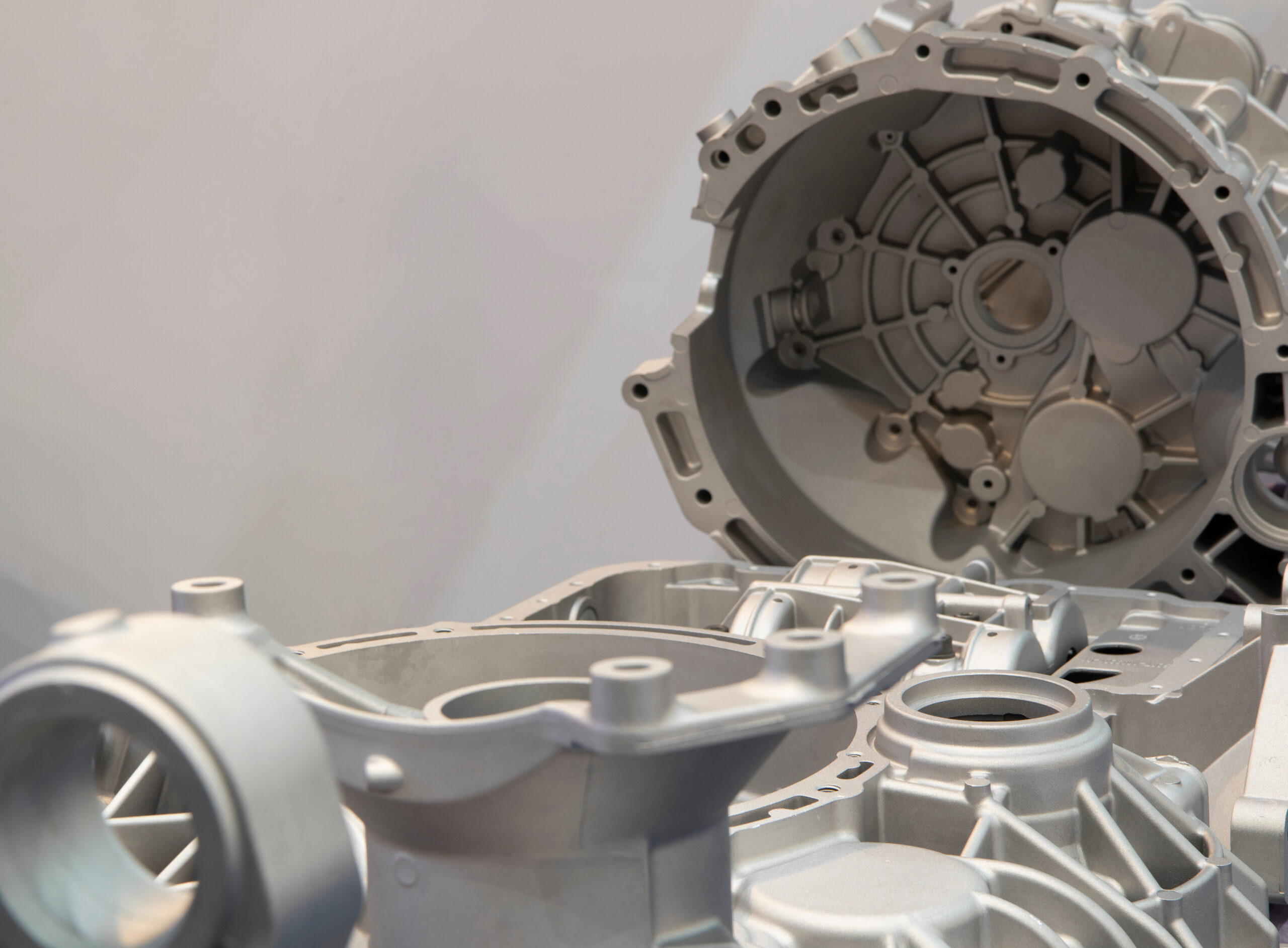
- Cost-efficient manufacturing process for high-volume production.
- Production lines are not labour intensive, almost everything runs automatically .
- Good surface finish (N8 or better) can be manufactured with smooth or textured surfaces, and are easily plated or powder coated.
- Very cheap additional machining cost, because often no secondary machining is needed.
- Long tool Life 150.000 – 200.000 parts of identical Die Castings can be produced from a Die tooling.
- Minimums of 500 up to 100,000 units per series
- Highly suitable for complex thin-walled parts.