3D Printed Cores for Castings
Why choose 3D Printed Cores for Castings for Rapid Prototyping Supply:
3D-printed cores for casting represent a revolutionary technology in the foundry industry, enabling the creation of complex and intricate core shapes that would be difficult, if not impossible, to achieve using traditional methods. These cores are particularly useful in metal casting processes for parts that require internal cavities or intricate geometries.
The 3D printing process builds foundry cores layer by layer from silica sand and a dry binding agent, directly from a CAD/CAM design. This eliminates the need for traditional core boxes and reduces the time and labour involved in creating cores manually.
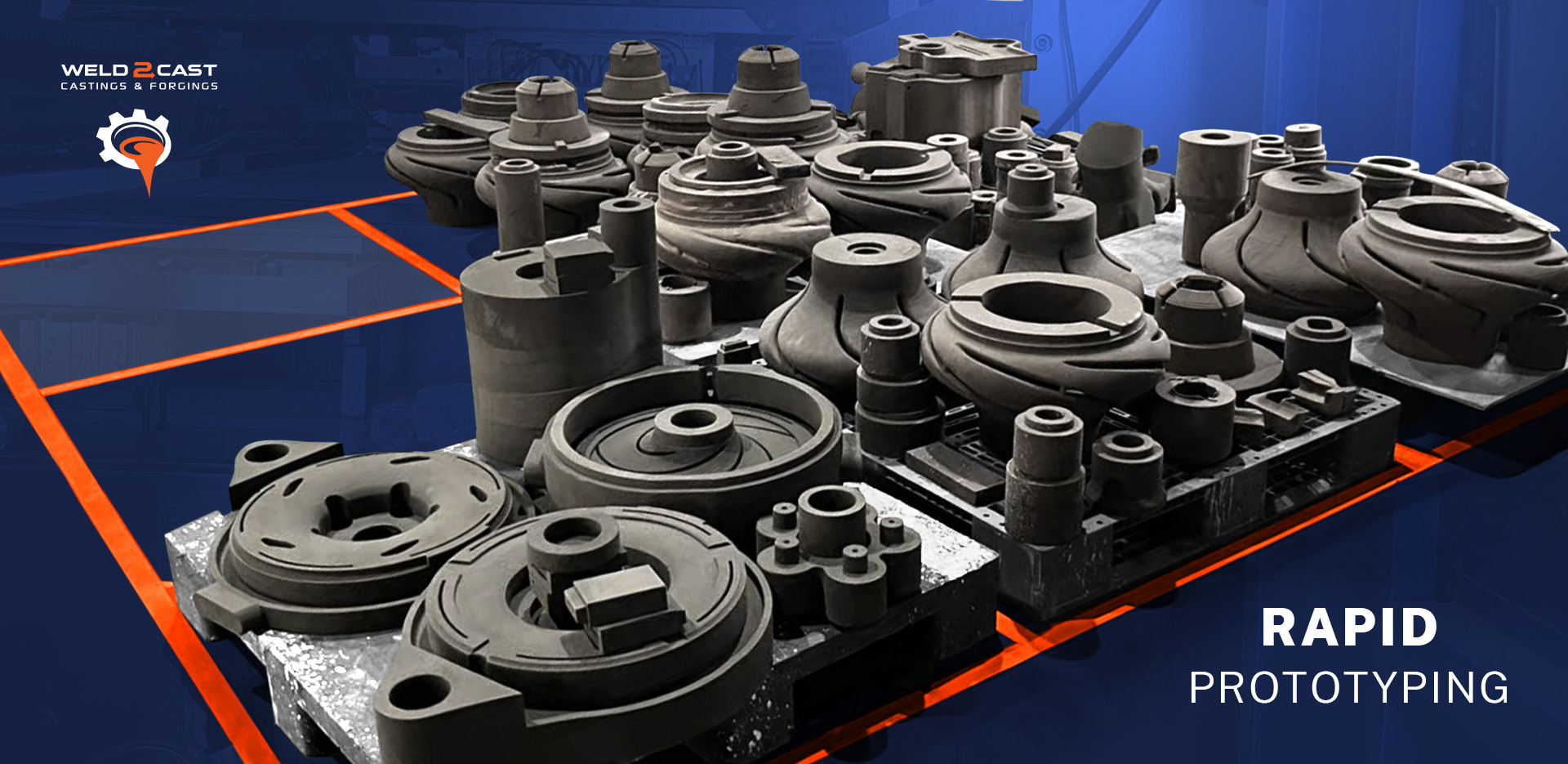
WELD2CAST’s 3D Printed Cores for Castings Benefits Include :
Complex Geometries and Design Freedom, that would be challenging or impossible to produce with conventional sand molding techniques.
Faster Production and Shorter Lead Times, 3D-printed cores can be produced in hours, directly from a digital design file.
Reduced Material Waste, 3D printing deposits material only where needed.
Customization and Flexibility, enabling customization for each project without the need for new molds or specialized tooling.
Reduced Tooling Costs, especially for low-volume production, prototypes, or parts requiring frequent design iterations.
Increased Precision and Accuracy, which leads to better casting quality
Faster Design Iterations, enabling faster testing of different concepts.
Improved Surface Finish, 3D-printed cores often result in a better surface finish for cast part, enhancing both the aesthetics and functionality of the final product.
Low-Volume Production and Prototyping, 3D-printed cores are ideal for cost-effective prototyping and small-batch production, allowing quick development and testing
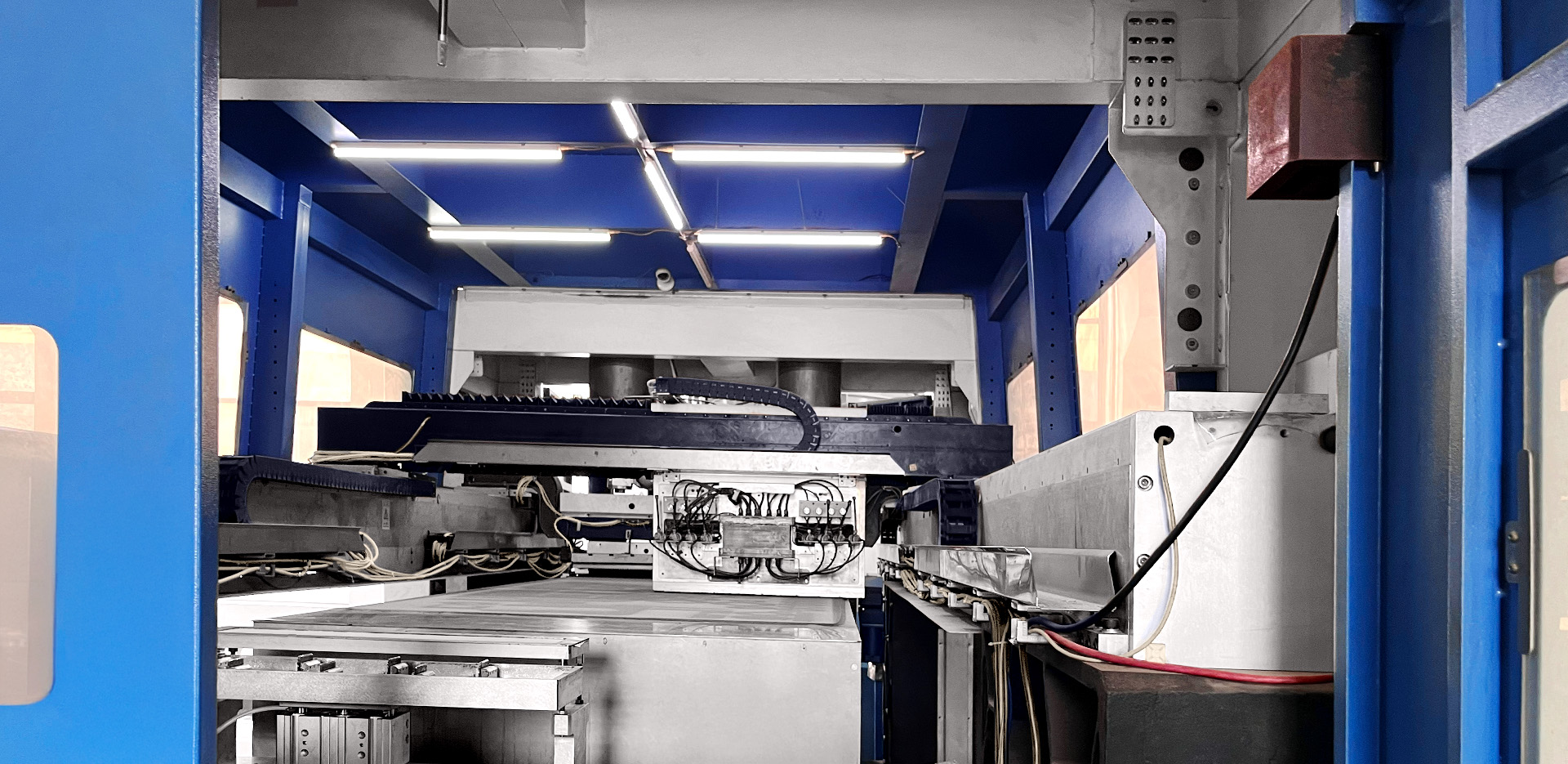
Conclusion:
3D-printed cores unlock a range of advantages in sand casting, including greater design flexibility, faster production, reduced costs, and improved casting quality. Whether for aerospace, automotive, energy, or high-performance manufacturing, this technology is perfect for industries that require complex geometries, customized low-volume production, and rapid prototyping. With 3D printing, the possibilities for innovation in casting are limitless.